Tin Plating
The tin plate process is used extensively to protect both ferrous and nonferrous surfaces. Tin is also widely used in the electronics industry because of its ability to protect the base metal from oxidation and corrosion.
Depending on the base material, tin is used as a metal plating to maintain or impart solderability. Valence has small tin reflow capability on site in Garden Grove, CA. This reflow process meets the requirements of ASTM-B-545 Type 1.
In tin electronic applications, 3% to 7% lead may be added to improve solderability and to prevent the growth of metallic whiskers which could cause electrical shorting. Valence operates a 90/10 and a 95/5 dull tin plating bath to meet this requirement.
RoHS (Restriction of Hazardous Substances) regulations enacted in 2006 require that the maximum percentage of lead used in dull tin plating not exceed 1%. Some exemptions have been issued to RoHS requirements in critical electronics applications due to failures which are known to have occurred as a result of tin whisker formation.
Valence can meet your RoHS requirements as well as any military specification.
Request a quote for tin plating your parts or components or contact us for more information.
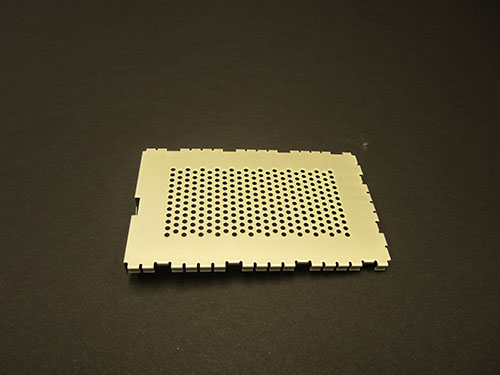
Tin Plate Process
Tin Plating
Tin is a very adaptable material with a wide range of useful uses in our daily lives. Tin cans, which are used to store a variety of foods and drinks, are common household items. Tin cans are actually made of sheet steel that has been coated with a thin layer of tin, a process known as tinplate.
Today, soldering applications use about half of all tin produced. Pewter, bronze, and phosphorous bronze are also made from tin. Sometimes tin salts are sprayed on window glass and windshields to give them an electrically conductive coating. Floating molten glass onto molten tin creates a flat surface, which is often used to create the window glass itself. Bells are frequently made of a metal alloy that contains both bronze and tin. Tin and tin alloys are also extremely valuable for electroplating, which is the process of applying a metal coating to a material’s surface using an electrical current.
In this article, we will discuss tin plating, its benefits, limitations, how to navigate the limitations, and the process of achieving a quality tin plate.
What Is Tin Plating?
Tin plating is an industrial procedure where a thin layer of tin is applied to metal objects. Steel, iron, and copper are just a few of the many base metals that can be processed using this method. For some applications, tin plating makes these metals look better while also enhancing their performance and tensile strength. Tinplate is the term used to describe a material that has had tin applied to a metallic base element.
The plating of metal food storage cans is arguably the most well-known use of tin plating. Additionally, tinplate is a typical material used to create pots, pans, and other cookware.
How Is Tin Plating Done?
Most metals can have tin electrodeposited on them. Let’s examine the specific elements of a successful tinplating process in more detail:
Cleaning
The substrate, which will receive the tin coating, must be thoroughly cleaned before being submerged in the plating solution. Cleaning gets rid of surface impurities like grease, oil, and other things that could hinder plating.
Cleaning is a multi-step process that varies slightly depending on the substrate’s makeup, how much dirt and debris it contains, and the kinds of cleaning tools that can be used. The cleaning procedure generally entails:
Electrolytic degreasing: Grease and oil that builds up in cracks, crevices, and other difficult-to-reach surface areas can be removed by submerging the substrate in an electrolytic solution.
Rinsing: Rinsing the substrate in water after electrolytic degreasing gets rid of any dirt and cleaning agent that may have remained on the surface.
Grit blasting: Grit blasting is the process of removing foreign material from a surface by projecting media such as crushed glass, aluminum oxide, silicon carbide, steel, corn cobs, or walnut shells using pressurized air.
Boiling: Without having to use chemical additives, boiling the substrate in water can be an efficient way to get rid of grease and oil.
Prepare The Bath
The preparation of an electrolytic solution, also referred to as a plating bath, comes next. Acid tin, alkaline tin, or methyl sulphonic acid solutions can be found in electrolytic tin plating baths. Tin is dissolved to produce positively charged ions that are suspended in a solution, along with other chemical additives, in a plating bath. The bath acts as the electrodeposition’s conductive medium.
Because acid baths have a higher deposition rate, they are typically used more frequently. While acid baths typically offer a uniform coating, they do not always consistently reach holes or other surface irregularities.
The Electrodeposition Procedure
The substrate is prepared for electrodeposition of the tin coating once it has been cleaned and submerged in the electrolyte bath. Usually, the item is positioned in the middle of the tank, which is made specifically to hold the electrolytic solution. The item serves as the cathode, the electrical circuit’s negatively charged electrode. The positively charged electrodes in the circuit, known as the anodes, are positioned close to the plating tank’s edge.
The plating bath must now be filled with a low-voltage DC current. DC current is produced by converting AC power through a device called a rectifier. Positively charged ions at the anode eventually move through the electrolyte in the plating bath toward the negatively charged cathode (substrate), where they are electrodeposited onto the surface as a result of the introduction of the electrical current. In order to complete the circuit, the current then flows back toward the anode.
Post Electroplating Process
Usually, post-treatment is not necessary after the tin plating process. In particular plating applications, passivation, which is the application of a thin coating of protective material, may be used to increase the reactive qualities of the tin or to offer additional corrosion protection.
In addition to using heat treatment, hydrogen embrittlement—a weakening of metal brought on by exposure to hydrogen—can also be avoided.
Types Of Tin Plating
There are three basic types of tin plating, all of which entail the application of an electrolytic tin solution to the metal object’s surface:
Barrel Plating
Placing the items in a specially made container, commonly known as a barrel, allows for barrel plating, which is typically used for smaller parts. While submerged in the electrolytic plating solution, the barrel slowly rotates.
Tin barrel plating is incredibly economical, though the plating procedure takes a while to complete.
Rack Plating
Rack plating is the method of choice for applying tin to larger or more delicate parts that may not be appropriate for barrel plating. Rack plating involves hanging the items on a rack and submerging them in the plating solution.
Rack plating offers greater control over plating thickness and has the potential to be more efficient at reaching cavities deep within the object than barrel plating, despite being more labor-intensive and, therefore, more expensive.
Vibratory Plating
Vibratory plating is another technique for delicate parts that involves putting the parts in a basket with metal buttons that also contains the electrolytic plating solution. The components move and come into contact with the metal buttons thanks to a generator’s vibrating action.
Tin plating using vibration is typically the most expensive method and necessitates a unique drying procedure that could result in the parts bending.
Benefits Of Tin Plating
The benefits of tin plating include:
Tin Plating Is Cheaper
In comparison to other metals, tin is very cheap. Tin plating is always preferred by manufacturers over other types of plating because it is equally effective but costs much less. Tin plating is the preferred technique, even though it can occasionally be less effective than other types of plating because the difference is so small.
Quality Shielding
When exposed to the environment, tin plating is frequently used as a practical defense against corrosion, oxidation, and erosion. Copper and other metals don’t react as much. This is avoided by applying a thin layer of tin, which also extends the product’s overall lifespan overall. The same is true of numerous other materials.
Clean Contact
Tin coats offer a good, clean contact surface that is ideal for conducting electricity in addition to shielding other metals. Tin plating is frequently used on conductors because it stops oxidation, which can lower their level of conductivity.
Corrosion Resistance
Tin electroplating is a fantastic technique for preventing corrosion in metals like iron or steel. These metals can be coated with tin to prevent oxidation and increase the shelf life of your products.
Although tin plating is the ideal plating solution for these kinds of industries, zinc plating is also frequently used to help with corrosion. However, zinc is known to be too toxic to be used in food or medical applications.
Solderability
Another great benefit of tin plating is that it can increase the solderability of a metal object, making it easier to weld it to another surface.
Here’s a summary of the benefits of tin plating. The fact that tin plating, also known as “tinning,” is a very economical process is probably the main justification. Tin is much less expensive than more expensive metals like gold, platinum, or palladium because it is so widely available. Tin also provides superior corrosion protection and excellent solderability.
When a matte or dull appearance is preferred, tin plating can produce a whitish-gray color. If more luster is desired, it can also create a shiny, metallic appearance. Due to tin’s reasonable level of conductivity, tin plating is useful in the production of various electronic components. The FDA also permits tin for use in the food service sector.
Common Problems With Tin Plating
Tin plating, like every other plating technique, is not without its own problems. Below are the problems you’re likely to encounter when tin plating:
Tin “Whiskers”
Long after the plating process has finished, the surfaces of pure-tin-plated objects can develop tiny, sharp protrusions known as whiskers. Although these microscopic metal fibers cannot be seen with the naked eye, they have the potential to seriously harm the finished product. As electrical conductors, whiskers have the potential to short-circuit electronic parts.
Tin whiskers have even been known to cause satellite failure, computer system failure, and disruptions in nuclear power plant operations. Tin whiskers have no known cause, and there is no known way to completely stop them from growing. Although this technique is far from foolproof, there has been some success in reducing the formation of tin whiskers by altering the crystalline structure of the tin deposit.
Lack Of Uniform Thickness
On the plated object, the tin may not always be applied evenly. It can occasionally be challenging to achieve the desired thickness, which is typically in the range of ten to twenty microns, depending on the shape and contour of the object.
Tin may be deposited with a greater thickness on the outer corners and a lower thickness in recessed areas when plating on metal objects with sharp corners. Relocating the anodes and changing the DC current’s density can frequently fix this.
Perishable Solderability
Despite the fact that tin-plated metals are renowned for having excellent solderability, this quality will deteriorate with time. Through proper deposit specification, suitable substrate preparation, and suitable plating component packaging, the soldering lifespan can be increased. It has been observed that sealing plated products in nitrogen-filled bags can extend their shelf life for solderability by ten times.
How To Navigate These Problems
Like every other problem out there, these tin plating problems have solutions. In order to prevent these problems, you should:
Our Plating Services
Our plating services include the following:
Cadmium Plating
Cadmium plating is a tough and versatile coating. The soft, attractive coating provides a favorable bonding surface for adhesions. It is also the preferred plating for salt-water environments due to its resistance to mold and bacteria
Chrome Plating
Chromium plating is effective at providing excellent hardness and lubricity, reducing friction, minimizing wear, and preventing galling. In environments with corrosion or abrasion, chrome plating can withstand the negative consequences of wear and tear.
Copper Plating
Copperplate has high electrical conductivity, exceeded only by silver plating. Copper is an excellent and inexpensive coating for many different uses that require conductivity or solderability. As a result of malleability and perfect adhesion, copper can maintain adhesion and serve as a base for added coating and plating.
Gold Plating
Gold plating advantages include good corrosion resistance and good solderability, and when alloyed with cobalt, it has very good wear resistance. Gold is commonly used in electrical switch contacts, connector pins and barrels, and other applications where intermittent electrical contact occurs. It is also used as a radiation shield in infrared reflectors and electronic satellite housings. Valence also offers immersion gold plating.
Manganese Phosphate
Manganese phosphate coating is a conversion coating, the formulation of which contains a manganese salt, phosphoric acid, and an accelerator. This process is done under high temperature and produces a surface that has good corrosion and wears resistance. Manganese phosphate coatings can retain oil and other lubricants.
Nickel Plating
Nickel plating provides exceptional hardness and corrosion/wear resistance. Nickel is one of the four ferromagnetic materials at room temperature and is a fairly active element. However, nickel deposits are slow to react in standard atmospheric environments due to the formation of a protective oxide surface providing excellent corrosion performance on most products.
Nickel Sulfamate
Nickel sulfamate is a plating process that provides a highly ductile plating surface with low internal stress. The versatility of the coating resists high temperatures, maintains high tensile strength, and provides ductility and elongation.
Ti-Cad Plating
Ti-Cad or titanium cadmium plating is a titanium cadmium combination plating that provides corrosion resistance on high-strength steel applications. It significantly reduces the negative consequences of hydrogen embrittlement.
Choose A Quality Plating Company
As was already mentioned, the ability to solder tinplated products is a perishable quality with a limited shelf life. By properly specifying the deposit, preparing the substrate, and packaging the plated components, Valence Surface Technology engineers can work with your business to help extend the soldering life of products. To stop the tin deposit from oxidizing, plated products can be packaged in sealed nitrogen bags, which are filled with pure nitrogen and heat-sealed. The solderability shelf-life can be increased using this method to more than ten times that of parts packed using conventional techniques.
Tin deposits have the capacity to develop filiform tin whiskers that spread from the deposit’s surface. Our company provides tin/lead plating services that are resistant to the possibility of whisker growth for applications where tin whiskers could adversely affect the functionality of the product. The reflow of tin deposits can also lessen, but not entirely prevent, the development of tin whiskers.
Consider A Tin-Lead Alloy For Tin Whisker Reduction
You should seriously consider a tin-lead plating alloy if tin whiskers are an issue in your manufacturing environment. Tin-lead is a great option when creating electronic components like printed circuit boards, connectors, and semiconductors because contrary to pure tin, it can be effective at preventing the growth of whiskers.
Strong acid solutions can be used to deposit a tin-lead alloy without the use of complexing agents because both metals have high hydrogen overvoltages.
Tin Alloy Plating
By co-depositing (alloying) tin with another metal or a number of other metals, one can improve the tin plating procedure. Tin alloys that are frequently used include:
A tin alloy can provide more corrosion protection than pure tin alone, in addition to reducing whisker. Tin lead also provides excellent solderability and can produce a softer, more ductile finish. Because of its ductility, tin-lead can prevent damage to the underlying metal during rigorous manufacturing processes such as stamping.
Tin-lead: Offers resistance to corrosion, excellent solderability, and the ability to create a soft, ductile finish while assisting in the prevention of tin whiskers.
Tin-copper: Increases the coating’s general strength, but it could also make it more brittle. It may also encourage the growth of tin whiskers and result in insufficient wetting for soldering applications.
Lead-tin-copper: The lead-tin-copper alloy is frequently used to lower friction on sliding engine bearings.
Tin-silver: Increases maximum service temperatures and overall mechanical strength, but the silver component can make this alloy prohibitively expensive for many businesses.
Tin-zinc: Provides a high melting point and superior fatigue strength but suffers from poor wettability and only moderate corrosion resistance.
Tin-bismuth: This alloy has excellent wettability, can reduce whisker formation, and is best suited for low-temperature plating applications.
Tin Plating Standards
ASTM B545
Class A – 0.0001-inch minimum, mild service conditions for applications where the significant surface is shielded from the atmosphere
Class B – 0.0002-inch minimum, mild service conditions with exposed significant surface
Class C – 0.00032-inch minimum (nonferrous), 0.0004-inch minimum (ferrous), moderate service conditions
Class D – 0.0006-inch minimum (nonferrous), 0.0008-inch minimum (ferrous), severe service conditions
Class E – 0.0012-inch minimum, very severe service conditions
Class F – 0.00006-inch minimum, service conditions similar to class A but for short-term contact applications and short shelf-life requirements
4.3.1 – Section Defines Matte Tin Electrodeposits
4.3.2 – Section Defines Bright Tin Electrodeposits
4.3.3 – Section Defines Flow Brightened Electrodeposits
6.8 – Class A and F coatings should have a nickel underplate of at least 1.3 um (50 uin) before tin plating if they won’t be exposed to solder temperatures. Prior to tin plating, substrates made of brass or other copper alloys containing more than 5% zinc must have a copper undercoating of at least 2.5um (100uin) or a nickel underplating of at least 1.3um (50uin) to prevent zinc migration and impaired solderability during service or storage. In some circumstances, a thicker nickel coating may be necessary for additional retardation (of zinc migration into the tin).
MIL-T-10727
Type I – Electrodeposited (Recommends referencing ASTM B545 for electrodeposits of tin)
Type II – Hot Dipped (Advanced Plating Technologies does not offer hot dip services)
Intended Uses per Section 6.1 of MIL-T-10727
- MIL-T-10727 cross references to ASTM B545, which outlines thicknesses for various service conditions in section 6, paragraph 6.1
- 0.0001-0.00025 inch for tin flashing of articles to be soldered
- 0.0002-0.0004 inch for articles to prevent galling or seizing
- 0.0003 inch minimum for articles generally plated to prevent corrosion of basis metals
- 0.0002-0.0006 inch for articles to prevent the formation of case hardening during nitriding
AMS 2408
3.1.1 Steel parts having a hardness of 40 HRC or higher and which have been ground after heat treatment shall be cleaned to remove surface contamination and stress relieved before preparation for plating. Unless otherwise specified, the stress relief shall be 275F +/- 25F for not less than 5 hours for parts with a hardness of 55 HRC or greater and 375F +/- 25F for not less than 4 hours for other parts.
3.2.1 Except as stated in 3.2.1.2 or 3.2.2, tin shall be electrodeposited directly on the base metal from a suitable tin plating bath.
3.2.1.2 Aluminum and aluminum alloys shall be zinc treated in accordance with ASTM B253 or other methods acceptable to the cognizant engineering organization prior to plating.
3.2.2 Prior to the electrodeposition of tin for solderability on aluminum or copper-zinc alloy parts, a copper plate shall be deposited to a thickness of 0.0002 to 0.0003 inch (5.1 to 7.6um)
3.4.1.1. Plate thickness may be specified by this specification number and a suffix number designating the minimum thickness in ten-thousandths of an inch (2.5um); thus, AMS 2408-1 designates a plate thickness of 0.0001 to 0.0003 inch, AMS 2408-6 designates a thickness of 0.0006 to 0.0008 inch, etc. A tolerance of 0.0002 inch will be allowed.
3.4.1.2. Where “tin flash” is specified, plate thickness shall be approximately 0.0001 inch.
Tin Plating For Aerospace
The bright tin plating process produces a material very suitable for aerospace applications, and the results are a bright silver finish. The procedure yields the same results as traditional tin plating, but the finished product has a much shinier appearance that is better for both decoration and practical use.
This kind of plating is frequently used to give all kinds of surfaces great solderability and respectable corrosion protection. Tin plating is frequently used in a wide range of industries, from the printed board industry to numerous areas of the food industry and for decorative purposes.
Because Type I or electrodeposited tin is more affordable when used for tin plating, we prioritize it at valence surface technologies. The finish also becomes much shinier, as we previously stated, all thanks to the whitish-gray color that is created by tin electrodeposits.
Where Is Tin Plating Most Commonly Used?
Military/defense – A successful military coating must address conductivity, insulation, hardness, ruggedness, oxygen deprivation and/or saturation, and exposure to different chemical and caustic environments, among other factors.
Medical – For all types of invasive and non-invasive medical instrumentation, tools, and equipment, our electroless nickel plating offers performance and a longer working life for parts and components.
Aerospace – We offer high-precision, high-performance nickel electroplating finishing services that meet or exceed the demanding standards of the aerospace industry in order to ensure operational safety and the best performance of critical parts and components.
Aviation – For the best corrosion resistance, we offer the highest-quality electroless nickel plating for aircraft, with perfect uniformity and consistency across the entire surface of the treated part.
Final Thoughts
The tin plate process is used extensively to protect both ferrous and nonferrous surfaces. Tin is also widely used in the electronics industry because of its ability to protect the base metal from oxidation and corrosion.
Depending on the base material, tin is used as a metal plating to maintain or impart solderability. Valence has a small tin reflow capability on-site in Garden Grove, CA. This reflow process meets the requirements of ASTM-B-545 Type 1.
In tin electronic applications, 3% to 7% lead may be added to improve solderability and prevent the growth of metallic whiskers, which could cause electrical shorting. Valence operates a 90/10 and a 95/5 dull tin plating bath to meet this requirement.
RoHS (Restriction of Hazardous Substances) regulations enacted in 2006 require that the maximum percentage of lead used in dull tin plating not exceed 1%. Some exemptions have been issued to RoHS requirements in critical electronics applications due to failures that are known to have occurred as a result of tin whisker formation.
Valence can meet your RoHS requirements as well as any military specification.
Request a quote for tin plating your parts or components, or contact us for more information.