Aerospace Anodizing In Pittsburgh
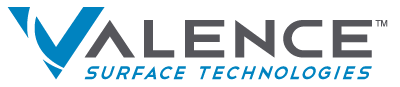
414 Innovation Drive
Blairsville, PA 15717
Valence Eastman
Aerospace anodizing plays a vital role in ensuring metal components’ structural integrity and long-term performance in demanding flight environments. In Pittsburgh, precision anodizing services support commercial and military aerospace programs by delivering high-durability finishes that improve corrosion resistance, wear protection, and surface bonding properties.
At Valence, our anodizing capabilities in Pittsburgh meet the rigorous standards of aerospace OEMs and regulatory bodies. We provide certified Type I, II, and III anodizing solutions backed by robust quality control systems, fast turnaround times, and expert-level process consistency, making us a trusted partner for mission-critical surface treatments.
Valence News
Corrosion Vs Oxidation: Key Differences In Metal Degradation And Protection Techniques
Corrosion vs oxidation—learn the key differences, effects on metals, and best protection techniques. Get expert insights from Valence today!
Tinned Copper Vs Bare Copper: Which Is Better For Electrical Applications?
Tinned copper vs bare copper—Valence breaks down the pros, cons, and best uses for each. Learn which is right for your electrical applications today!
Is Anodized Aluminum Safe? Exploring Its Uses And Benefits In High-Performance Industries
Is anodized aluminum safe? Learn about its uses and benefits in high-performance industries. Understand its safety and applications.
Does Nickel Rust? Understanding Nickel’s Resistance To Corrosion In Aerospace Applications
Does nickel rust? Learn how nickel resists corrosion in aerospace applications. Valence breaks it down—read now for key insights!
What Is Aerospace Anodizing?
Aerospace anodizing is a highly controlled electrochemical process used to enhance the surface properties of aluminum and its alloys, which are standard materials in the aerospace industry. The process involves submerging the aluminum component in an electrolytic bath and applying an electric current, which causes an oxide layer to form on the surface. This oxide layer is not simply a coating; it becomes an integral part of the metal itself.
Why Choose Valence For Aerospace Anodizing In Pittsburgh
When selecting a partner for aerospace anodizing in Pittsburgh, precision, reliability, and technical expertise are paramount. Surface treatments for critical aerospace components require more than routine processing—they demand a commitment to quality, strict adherence to specifications, and a deep understanding of evolving standards in aviation, defense, and space.
Unmatched Industry Experience
Valence brings decades of hands-on expertise in aerospace anodizing, supporting legacy and next-generation platforms. Pittsburgh’s facilities are fully certified to meet NADCAP, AS9100, and customer-specific quality systems. This deep industry knowledge translates into consistent finishes, reduced turnaround times, and clear communication throughout every project phase.
Integrated Capabilities Across The Supply Chain
Complete in-house capabilities eliminate the need to coordinate across multiple vendors. Valence provides a seamless finishing experience by integrating anodizing, chemical processing, non-destructive testing, and painting under one roof. This streamlined process enhances traceability, quality control, and logistics efficiency for aerospace components of all sizes and geometries.
Commitment To Precision And Consistency
Every component is processed using digitally monitored parameters, automated chemical controls, and strict process validation. From uniform anodic layer thickness to precise masking, Valence ensures adherence to the tightest engineering tolerances and specifications required by the aerospace industry.
Adaptability For New Technologies
Innovation is built into every process. Valence continuously invests in advanced anodizing solutions—including Type I, II, and III finishes, chromate alternatives, and hybrid technologies—to meet evolving materials and regulatory requirements. Pittsburgh facilities are equipped to support the next generation of aerospace manufacturing with scalable, compliant surface treatments.
Unlock Aerospace Excellence With Valence: Your Trusted PartnerAt Valence Surface Technologies, we’re not just a finishing company; we’re your aerospace surface finishing partner. Discover the benefits of our unique integrated solution:
Join the aerospace elite and elevate your projects to new heights with Valence. |
Comprehensive Aerospace Anodizing Services
Valence Surface Technologies offers full aerospace anodizing services tailored to the industry’s precise needs. Each process is executed precisely to enhance performance, ensure durability, and meet stringent aerospace standards.
Type I – Chromic Acid Anodizing
- Application: Ideal for thin coatings where minimal surface impact is required.
- Benefits:
- Excellent corrosion resistance.
- Superior adhesion for primers and paint.
- Minimal dimensional change, perfect for tight tolerances.
- Common Uses: Aircraft skins, structural components, and assemblies.
Type II – Sulfuric Acid Anodizing
- Application: The most versatile anodizing method, offering durability and customization.
- Benefits:
- Customizable finishes with optional coloring.
- Excellent corrosion protection.
- Balanced wear resistance for functional and decorative parts.
- Common Uses: Fasteners, interior components, and parts requiring aesthetic finishes.
Type III – Hard Coat Anodizing
- Application: Designed for parts exposed to extreme wear and demanding conditions.
- Benefits:
- Thick, highly durable coating for abrasion and impact resistance.
- Exceptional thermal insulation and corrosion resistance.
- Enhanced lifespan for critical components.
- Common Uses: Hydraulic cylinders, landing gear, and engine components.
Other Finishing Services We Provide
Aerospace components require more than just anodizing to meet the aviation, defense, and space sectors’ extreme performance, safety, and durability standards. In addition to offering expert aluminum and titanium anodizing with a range of finishes, Valence provides a complete suite of integrated services to ensure total compliance and performance across complex aerospace assemblies.
Our anodizing process is engineered for consistency and precision, and our Los Angeles facility reflects our commitment to delivering full-spectrum surface treatment solutions from a single, trusted partner.
Chemical Processing
Critical pre-treatment services such as etching, passivation, and degreasing are all part of Valence’s comprehensive chemical processing offerings. These methods ensure optimal surface preparation for downstream finishing, providing a clean, active substrate that enhances adhesion and long-term corrosion resistance, which is especially vital for aerospace-grade materials.
Paint And Coatings Application
Valence applies high-performance primers and topcoats that deliver both protective and aesthetic value. Aerospace coating systems are applied using automated and manual techniques for precise, uniform results that comply with aerospace OEM and military specifications, including color, gloss, and environmental resistance standards.
Non-Destructive Testing (NDT)
Safety and performance begin with verification. Valence offers NDT solutions such as dye penetrant inspection, magnetic particle testing, and ultrasonic methods to detect surface and subsurface flaws. These inspection protocols support certification and compliance efforts while maintaining the structural integrity of critical parts.
Precision Masking
Precision masking ensures that only designated areas receive surface treatments. Using aerospace-approved materials and skilled technicians, Valence protects tight-tolerance features, mating surfaces, and sensitive zones throughout the finishing process. This targeted approach preserves functional integrity and eliminates the risk of rework.
Who We Serve
The demand for high-performance aerospace anodizing in Pittsburgh is driven by industries with exacting technical requirements and zero tolerance for failure. As materials, regulations, and engineering specifications evolve, the need for expertly executed surface finishing becomes even more essential. The following sectors continue to rely on the advanced anodizing capabilities delivered by our team at Valence.
Aviation Industry
Aircraft manufacturers and Maintenance, Repair, and Overhaul (MRO) providers rely on our precise anodizing processes to extend the life and reliability of critical components. From fuselage skins and landing gear to interior hardware, each part receives a corrosion-resistant, uniform finish that meets the tight tolerances and rigorous quality controls required for commercial and military aviation.
Defense Sector
Anodizing solutions for the defense industry are engineered to withstand the harshest operational environments. Our work supports air, land, and sea applications by delivering durable, traceable finishes that comply with military specifications, including MIL-A-8625 and other aerospace directives. These processes are essential for maximizing part life and ensuring mission readiness.
Space Exploration
The challenges of space demand materials that can perform flawlessly under extreme conditions. Our anodizing treatments provide essential protection against thermal cycling, oxidation, and outgassing—factors critical for components used in launch vehicles, satellites, and orbital platforms. Our commitment to consistency and precision supports the success of every mission from fabrication to flight.
Benefits Of Aerospace Anodizing
Aerospace anodizing is a critical process in manufacturing aircraft and spacecraft components. This electrochemical process converts the metal surface into a durable, corrosion-resistant, and aesthetically pleasing finish.
Key Benefits Of Aerospace Anodizing:
- Corrosion Resistance: Protects aluminum components from harsh environmental conditions, including salt spray, humidity, and extreme temperature fluctuations.
- Wear Resistance: Enhances components’ surface hardness and durability, reducing wear and tear.
- Improved Adhesion: Provides a superior bonding surface for paints and coatings, ensuring long-lasting protection.
- Electrical Insulation: Offers excellent electrical insulation properties, which are crucial for sensitive electronic components.
- Enhanced Appearance: Provides a range of decorative finishes, from natural aluminum to vibrant colors.
Aerospace Anodizing Applications
Aerospace anodizing is a critical process in manufacturing aircraft and spacecraft components. This electrochemical process converts the metal surface into a durable, corrosion-resistant, and aesthetically pleasing finish. Key Applications of Aerospace Anodizing:
Aircraft Structures
- Fuselage: Anodized aluminum provides lightweight, strong, and corrosion-resistant structural components.
- Wings: Anodizing protects wing structures from environmental factors and improves their fatigue life.
- Landing Gear: Anodized components enhance the durability and corrosion resistance of landing gear, ensuring safe and reliable operation.
Engine Components
- Engine Housings: Anodized housings protect critical engine components from high temperatures, corrosive gases, and mechanical stress.
- Fan Blades: Anodized fan blades improve their wear and corrosion resistance, enhancing engine performance and efficiency.
Electronic Enclosures
- Avionics Enclosures: Anodized aluminum enclosures protect sensitive electronic components from electromagnetic interference, thermal stress, and environmental factors.
- Control Panels: Anodized control panels provide a durable, corrosion-resistant, and aesthetically pleasing surface.
Other Applications
- Fasteners: Anodized fasteners offer excellent corrosion resistance and improved thread engagement.
- Hardware: Anodized hardware, such as brackets and fittings, provides long-lasting performance in harsh environments.
Pricing Information For Aerospace Anodizing In Pittsburgh
Navigating the costs associated with aerospace anodizing in Pittsburgh requires a clear understanding of multiple factors influencing pricing structures. Companies seeking top-tier surface finishing services should know that pricing is not just about the base process, but also the quality standards, certifications, and value-added capabilities included in the offering.
Factors That Influence Anodizing Costs
The cost of aerospace anodizing can vary significantly based on several technical criteria:
- Material Type: Different aluminum alloys respond uniquely to anodizing processes, impacting chemical consumption and processing time.
- Coating Thickness Requirements: Aerospace specifications often demand precise thickness tolerances, with tighter controls resulting in higher costs.
- Component Size and Geometry: Larger or more complex parts require more resources for masking, fixturing, and even bath sizes.
- Volume of Work: Bulk orders may yield efficiencies and price breaks, whereas small runs or prototypes typically incur higher per-unit costs.
- Certifications and Quality Standards: Meeting NADCAP or other aerospace-grade certifications increases inspection, documentation, and process control expenses.
Typical Pricing Models
Aerospace anodizing providers in Pittsburgh commonly use one of several models when quoting projects:
- Per-Part Pricing: Ideal for small batches or irregular, low-volume orders.
- Square Footage or Weight-Based Pricing: Commonly used for larger production runs, this model ties cost directly to the material processed.
- Custom Quotations: Highly complex assemblies or multi-process jobs are quoted based on unique engineering and process requirements.
Additional Cost Considerations
Beyond the base price for anodizing, there are often supplementary charges that can affect the overall investment:
- Expedited Lead Times: Rush orders may command premium rates due to accelerated scheduling and overtime labor.
- Special Handling or Masking: Protective masking for selective anodizing or intricate component features can add significant labor costs.
- Testing and Certification Documentation: Meeting rigorous aerospace traceability and testing protocols introduces extra quality assurance charges.
When planning an aerospace anodizing project in Pittsburgh, a transparent discussion of technical requirements with service providers is key to obtaining accurate, reliable pricing.
Exploring Valence Surface Technologies’ Locations
Valence Surface Technologies is proud to offer a network of facilities strategically located across the United States to provide aerospace and defense industries with top-quality surface treatment services. Here’s a closer look at the regions we serve and the specialized services we offer at each of our locations:
Eastern Region
Valence Surface Technologies operates multiple facilities in the Eastern U.S. that service the aerospace and defense markets. With locations in Eastman, Georgia, Grove, Oklahoma, Blairsville, Pennsylvania, West Springfield, MA, and Wichita, Kansas, we provide a comprehensive set of surface treatment services.
Our services in this region include:
- Nondestructive Testing (NDT): Advanced methods for detecting material defects, ensuring the integrity of parts before they are put into operation.
- Anodizing: Essential for providing corrosion resistance and aesthetic finishes, particularly for aluminum parts.
- Paint/Spray Coatings: Customized coatings that offer protection against environmental factors and improve the visual appearance of components.
- Shot Peening: A process used to enhance the fatigue life of metal parts by creating compressive stress on the surface.
- Bond Primer: Specialized primers that promote better adhesion of topcoats, ensuring long-lasting durability.
From very small components to parts over 20 feet in length, our Eastern Region facilities are equipped to handle a wide range of part sizes and offer the highest quality standards for aerospace and defense applications.
Northwest Region
Valence’s Northwest Region facilities in Seattle, Washington and Everett, Washington serve the aerospace and defense markets from British Columbia, Canada to Oregon. These locations are strategically positioned to service both the Pacific Northwest and Western Canada, providing full-service aerospace treatments with advanced capabilities.
Our services in this region include:
- Nondestructive Testing (NDT): Ensuring that parts are structurally sound and free from defects before they are utilized in mission-critical applications.
- Anodizing: Providing durable finishes that increase the lifespan of components by enhancing corrosion resistance.
- Paint/Spray Coatings: A vital service for aerospace parts requiring weather-resistant and visually appealing finishes.
- Shot Peening: Vital for ensuring the fatigue resistance of high-stress components, such as aircraft fuselages and engines.
- Bond Primer: Applied to ensure superior adhesion of the topcoats, leading to longer-lasting finishes and superior performance.
Our Northwest Region facilities are fully equipped to handle parts ranging from small components to those up to 30 feet in length. This capacity allows us to meet the needs of various clients in the aerospace and defense industries.
Southwest Region
In the Southwest Region, Valence operates a cutting-edge facility in the greater Los Angeles area, covering California, Arizona, Nevada, and Utah. This region is a hub for aerospace and defense, and our facility in Los Angeles is one of the leading providers of surface treatments in the Western United States.
Our services in this region include:
- Nondestructive Testing (NDT): Ensuring that critical aerospace components meet the highest safety and reliability standards.
- Anodizing: Offering protective coatings for aluminum and other metals that are essential for aerospace parts exposed to harsh environments.
- Plating: We provide a range of plating services that offer corrosion resistance, wear resistance, and improved conductivity for aerospace components.
- Paint/Spray Coatings: Ensuring that parts receive the perfect finish to meet both performance and aesthetic requirements.
- Shot Peening: Used to improve the strength of aircraft parts, prolonging their service life and enhancing their reliability.
- Bond Primer: A key service for ensuring the longevity of topcoats and improving paint adhesion.
Our Southwest Region facility can handle parts up to 25 feet in length, giving us the flexibility to treat both large and small components. Whether you need high-end coatings, advanced testing, or specialized surface treatments, our Los Angeles location offers the experience and facilities to meet your needs.
Contact Valence Surface Technologies Today
Valence Surface Technologies offers advanced solutions backed by rigorous quality standards and industry expertise for exceptional aerospace anodizing services in Pittsburgh. Our precision finishing ensures your components meet strict aerospace requirements for durability and performance. Connect with our team to discuss how we can support your projects with reliable, customized anodizing services.
Frequently Asked Questions About Aerospace Anodizing In Pittsburgh
Can aerospace anodizing be performed on all metals?
No, aerospace anodizing is specifically designed for aluminum and its alloys. The process forms a protective oxide layer, enhancing corrosion resistance and surface hardness. Other metals, such as steel or titanium, require different surface finishing methods. Valence focuses on industry-compliant methods for aluminum components, ensuring optimal protection and performance.
How long does the anodizing process take?
The anodizing process timeline depends on aerospace components’ size, complexity, and volume. Small batches can often be completed within a few days, while larger or more intricate parts may require more time. At Valence, we leverage streamlined, integrated processes to deliver efficient turnaround while maintaining the highest quality standards.
Can anodizing be applied to aerospace components of any size?
Anodizing can be adapted for a wide range of component sizes, from small fasteners to large structural assemblies. Valence’s Pittsburgh Anodizing facilities are equipped to handle various dimensions and adhere to precise aerospace tolerances and requirements.
Is aerospace anodizing environmentally friendly?
Aerospace anodizing processes at Valence utilize advanced water treatment systems and environmentally responsible practices to minimize waste and pollution. While traditional anodizing uses chemicals, advancements in process control and waste management enable us to meet or exceed all regulatory standards for environmental sustainability.
How do I choose the right anodizing process for my aerospace application?
Selecting the right process depends on performance requirements such as corrosion resistance, wear resistance, conductivity, and appearance. The most common anodizing processes (Type I, II, and III) offer different characteristics. Valence’s technical experts can help evaluate your application and recommend the ideal process for your aerospace needs.
What are the costs associated with aerospace anodizing in Pittsburgh?
Costs are determined by component size, complexity, required anodizing type, volume, and any specialized certifications. As Pittsburgh’s premier provider of aerospace anodizing, Valence offers competitive, value-driven pricing tailored to the aerospace and defense sectors. For a precise quote, contact our team with your project specifications.